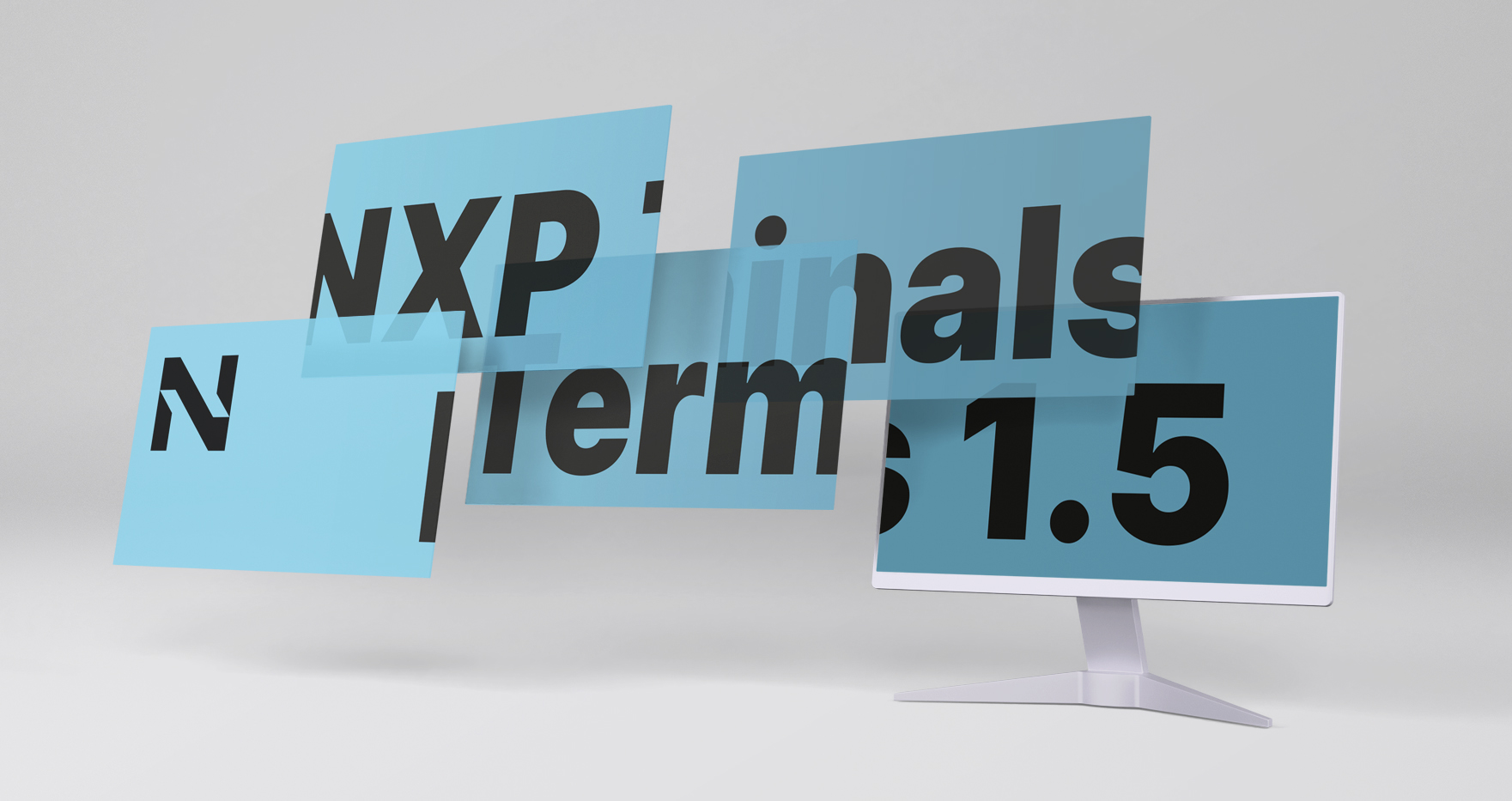
NextPort Launches NXP Terminals v1.5
NextPort has released NXP Terminals v1.5, introducing enhanced 3D visualization, smarter alarm filtering, and new live performance dashboards to make terminal operations more intuitive, responsive, and data-driven.
We’re pleased to announce the release of NextPort’s NXP Terminals v1.5, which includes a targeted set of improvements that streamline how users interact with the platform. These updates are aimed at making terminal operations more intuitive, insightful, and responsive. From real-time 3D visualization to enhanced alarm management, this release reflects our ongoing commitment to providing our users with innovative new ways of managing terminal operations.
Some of the new features included in the update are:
TopView — 3D Visualization
3D Visualization is now available in our TopView application, offering real-time, interactive, and spatially accurate views of terminal operations. Users are now able to visualize equipment and vessels in motion with enhanced detail and scale accuracy.
Key Benefits:
• Real-time, 3D monitoring of terminal equipment.
• Interactive features like click and hover for CHEs, and follow modes for TTs.
FlowOps — Alarm filtering by role and type
FlowOps’s historical alarms tab now better aligns with user roles, only displaying alarms that are relevant to each user. Additionally, users now have the ability to filter by alarm type as well as by name.
Key Benefits:
• Cleaner and more relevant alarm views for each user.
• Improved usability and faster access to critical alerts.
• Enhanced filtering for better operational visibility.
LeanIQ — New Live Performance Dashboard
Updates to the LeanIQ application now include a set of new dashboards as well as performance improvements. These dashboards are fully integrated with Power BI pipelines and dataflows.
Key Benefits:
• Dashboards are now aligned with shift times for improved workflow visibility.
• New versions of the “Performance” and “Alarms” live dashboards are now available.
NextPort Terminals v1.5 is another step forward in building a more integrated, data-driven terminal environment. These updates are designed to provide greater clarity for users, increase system responsiveness, and support smoother terminal operations.